摘要:基于熱傳遞原理,設(shè)計(jì)了一種大量程氣體流量傳感器。 采用FLUENT進(jìn)行結(jié)構(gòu)的仿真.結(jié)合權(quán)重法確定傳感器的結(jié)構(gòu)模型。研究了傳感元件的溫度特性.確定了傳感器的工作狀態(tài)。設(shè)計(jì)了傳感電路,對(duì)傳感器進(jìn)行了自動(dòng)溫度補(bǔ)償。測(cè)量中采用兩種不同的測(cè)量原理.使傳感器能夠檢測(cè)微小流量和中、大流量.提高了傳感器的測(cè)量范圍。實(shí)驗(yàn)結(jié)果表明該傳感器測(cè)量流量量程為0.14 m'/h~ 130 m'/h,測(cè)量誤差優(yōu)于1.5%。
熱式氣體流量傳感器是利用熱傳遞原理實(shí)現(xiàn)對(duì)氣體質(zhì)量流量的直接測(cè)量",其按結(jié)構(gòu)可分為熱分布型和浸人型。熱分布式型氣體流量傳感器可測(cè)量低流速微小流量鬥;浸人型氣體流量傳感器主要應(yīng)用于中、大管徑的較高流速測(cè)量,而對(duì)于低流速氣體的測(cè)量精度和靈敏度都較低。采用5個(gè)熱電阻PT1000 集成于同-基片的傳感元件,通過(guò)傳感電路設(shè)計(jì),使得氣體流量傳感器在小流量時(shí)采用熱分布型測(cè)量原理,在大流量測(cè)量時(shí)采用浸人式測(cè)量原理,從而實(shí)現(xiàn)了流量的大量程測(cè)量。同時(shí),由于該傳感器放置在管道內(nèi)部,因此傳感元件周?chē)牧鲌?chǎng)及流速大小將較大影響流量測(cè)量的性能。因此,首先對(duì)傳感器結(jié)構(gòu)進(jìn)行仿真,通過(guò).Solidworks軟件設(shè)計(jì)傳感器的9種結(jié)構(gòu)模型引,采用FLUENT仿真技術(shù)獲得不同傳感器結(jié)構(gòu)模型的管內(nèi)流場(chǎng)等速線水平剖面圖及管內(nèi)傳感元件截面的面平均速度,并結(jié)合權(quán)重法對(duì)仿真數(shù)據(jù)進(jìn)行處理,確定傳感器系統(tǒng)結(jié)構(gòu)模型。然后研究了傳感器的溫度特性[4],設(shè)計(jì)了傳感測(cè)量電路,實(shí)現(xiàn)對(duì)氣體在大量程范圍內(nèi)流量正確的測(cè)量。
1測(cè)量原理
氣體流量傳感器是在不同流量段分別采用熱分布型和浸人型的測(cè)量原理。熱式氣體傳感器的傳感元件置于管道中心[5],傳感元件如圖1所示。管道中沒(méi)有氣體通過(guò)時(shí),管道內(nèi)的溫度場(chǎng)是對(duì)稱(chēng)的。熱電阻R.、R。、R、R, ,作為熱源和溫度傳感器,R。用于氣體介質(zhì)溫度的測(cè)量。當(dāng)有微小氣體流過(guò)時(shí),上游熱電阻R.R,的溫度下降比下游熱電阻R、R,明顯,氣體將上游的熱量帶到下游,引起3管道內(nèi)部溫度場(chǎng)變化61,則氣體的質(zhì)量流量

式中E為單位時(shí)間內(nèi)輸出流量計(jì)的電功率,c,為被測(cè)氣體的比定壓熱容,ΔT為上下游溫差
隨著氣體流速的增加,氣體的流動(dòng)引起熱電阻Rs1、Rs2. s3、Rs4、溫度的變化,電路提供給四個(gè)電阻的3電功率等于氣體流動(dòng)對(duì)熱換流帶走的熱量,即

2熱式氣體傳感器系統(tǒng)結(jié)構(gòu)的設(shè)計(jì)
由于傳感元件通過(guò)圓柱形支架固定在管道內(nèi)部,圓柱體開(kāi)一矩形孔用于傳感元件測(cè)量氣體流量,見(jiàn)圖2所示。傳感元件周?chē)牧鲌?chǎng)對(duì)傳感器的靈敏度和重復(fù)性影響較大。同時(shí),傳感器的壓損也是一個(gè)重要的評(píng)價(jià)指標(biāo)。因此,需要對(duì)傳感器開(kāi)孔尺寸進(jìn)行仿真研究,以獲得理想的結(jié)構(gòu).
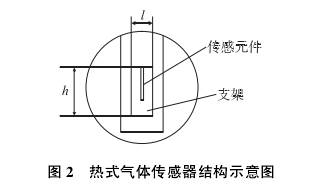
首先采用Solidworks軟件對(duì)氣體傳感器模型進(jìn)行建立,管道口徑為50 mm,管道長(zhǎng)度為130 Imm,管道中支架為小圓柱體,直徑為12mm[7].
將網(wǎng)格文件導(dǎo)入FLUENT軟件進(jìn)行仿真并保證各模型有相同的邊界條件,設(shè)定管道內(nèi)流體介質(zhì)為空氣,人口速度取10 m/s,根據(jù)式(3)求出管道雷諾數(shù)Re=337 84, 因此粘性模型為k-epsilon。 為了防止壁面有邊界層使得流體粘附管道,壁面選擇Moving wall。

式中V為入口速度,D為管道直徑,η, 為壓強(qiáng)為101.325 kPa、 溫度為20 C的條件下空氣的運(yùn)動(dòng)黏度根據(jù)式(4)計(jì)算出湍流強(qiáng)度1=4.345%[8]。

氣體傳感器插入管道中測(cè)量氣體的流速,會(huì)對(duì)氣體的流場(chǎng)有一定的擾動(dòng),不同的傳感器模型對(duì)流場(chǎng)的擾動(dòng)也不同[9]。因此需對(duì)傳感器模型的尺寸進(jìn)行設(shè)計(jì)仿真,選擇最佳模型。如圖2所示,傳感元件置于管道中,傳感元件長(zhǎng)7 mm,寬2.4 mm,厚0.15 mm。設(shè)計(jì)矩形孔的尺寸,1分別取3 mm、4 mm、5 mm,h分別取9 mm、10 mm、11 mm,共9種模型,研究不同模型對(duì)流場(chǎng)產(chǎn)生的影響。
采用FLUENT軟件10-1]1分別對(duì)這9種模型設(shè)置相同的邊界條件,進(jìn)行數(shù)值模擬計(jì)算。分別計(jì)算傳感元件不同位置的平均速度。選取傳感元件中心截面的編號(hào)為plane-5。按軸向方向在plane-5前后分別依次取5個(gè)截面,前面兩截面平行距離為0.24 mm,分別編號(hào)為plane-0, plane- 1, plane-2...共11個(gè)截面,如圖3所示,這些截面上的面平均速度可通過(guò)數(shù)值計(jì)算獲得。
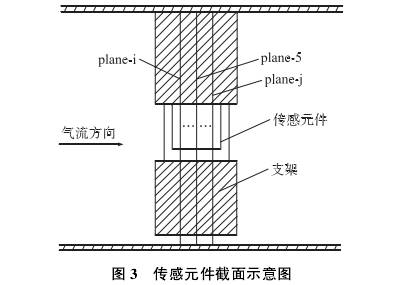
圖4所示為幾種矩形孔的管內(nèi)流場(chǎng)等速線水平剖面圖
從圖4可以看出,矩形孔的面積越大,傳感器前后的漩渦區(qū)越小,流場(chǎng)分布均勻,這是因?yàn)榫匦慰椎拿娣e越大,對(duì)流體的阻礙作用越小,對(duì)管道內(nèi)的流場(chǎng)影響越小[12]圖5表示9種不同傳感器模型11 個(gè)截面的面平均速度分布圖。
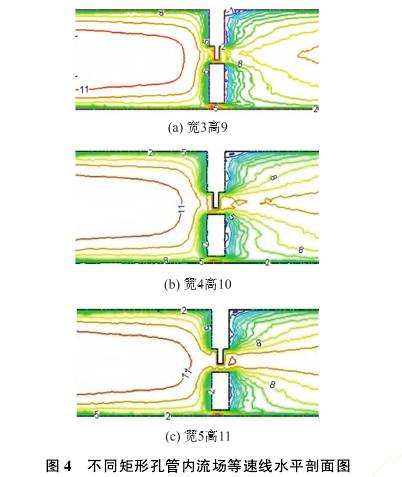
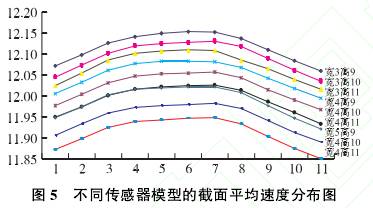
從圖5可以看出,矩形孔的面積越小,其面平均速度越大,但對(duì)流體的阻礙作用變大,使得流體的能量損失多。對(duì)于管內(nèi)的傳感元件,11個(gè)截面的面平均速度分布越穩(wěn)定,管內(nèi)速度分布的變化越小,對(duì)流場(chǎng)的擾動(dòng)越小。由式(5)貝塞爾公式求出標(biāo)準(zhǔn)偏差,度量數(shù)據(jù)分布的分散程度
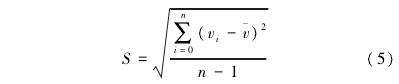
式中v;分別為第i截面的面平均速度,0為11 個(gè)截面平均速度的平均值,n為11。
表1為9種不同傳感器模型的0值、S值和壓損,這三個(gè)因素決定了傳感器模型的尺寸選擇,0值越大則量程比越大,S值和壓損越小則流體通過(guò)傳感器時(shí)損失的能量越小,流體分布也越穩(wěn)定。從表1可以看出,矩形孔的面積越大,值越小,而s值和壓損越小。可以看出壓損最大值與最小值相差約0.84 p,且對(duì)傳感器評(píng)定影響不大,在評(píng)定時(shí)可以忽略壓損這個(gè)因素,因此可通過(guò)權(quán)重[1”]來(lái)評(píng)定0值和S值在整體評(píng)價(jià)中的相對(duì)重要程度,并根據(jù)式(6)計(jì).算出綜合評(píng)價(jià)值,從而確定傳感器的模型

式中Vk為綜合評(píng)價(jià)值,wk為權(quán)重,xk為各因素的數(shù)值,k=1,2,3,4,5,6,7,8,9。
用算術(shù)平均法計(jì)算各因素的平均數(shù)x。和標(biāo)準(zhǔn)差sk,根據(jù)式(7)計(jì)算出各因素的標(biāo)準(zhǔn)差系數(shù),它反映各因素的相對(duì)變異程度
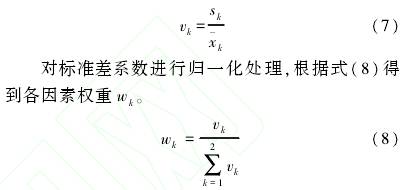
根據(jù)式(7)、(8)計(jì)算出二個(gè)因素的?k值和wk值,并根據(jù)式(6)計(jì)算出9種模型對(duì)應(yīng)的Vk 值,如表1所示口
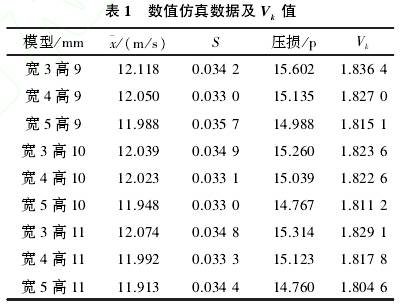
根據(jù)表1的V,值,可以確定寬3高9的模型為最佳模型。
3傳感元件溫度特性的研究
氣體經(jīng)過(guò)傳感元件表面時(shí)會(huì)帶走熱量從而引起測(cè)量電路電壓信號(hào)的變化,當(dāng)傳感元件上的熱電阻Rs1、Rs2、Rs3和Rs4與氣體溫差較小時(shí),傳感元件靈敏度會(huì)降低,但電流過(guò)大時(shí)會(huì)損壞傳感元件并增加電路的功耗,因此需對(duì)傳感元件的溫度特性進(jìn)行研究4],圖6為傳感元件溫度特性研究實(shí)驗(yàn)圖。
傳感元件放置在溫度可調(diào)的恒溫箱中,電路加恒定的電壓10 V ,在不同的工況條件下調(diào)節(jié)電位器的大小使電流保持恒定,并測(cè)量傳感元件的電壓V,然后計(jì)算傳感元件相應(yīng)電路的阻值和工作溫度。實(shí)驗(yàn)中恒溫箱型號(hào)為GHX高溫恒溫試驗(yàn)箱,電壓由可調(diào)直流穩(wěn)壓電源提供,型號(hào)為MPS- 3003L-3,電壓表型號(hào)為VC9807A。首先從低到高調(diào)節(jié)恒溫箱溫度并調(diào)節(jié)電位器大小使電流接近于6.2 mA,同時(shí)測(cè)量對(duì)應(yīng)溫度下熱電阻兩端的電壓。在同一溫度記錄3個(gè)數(shù)據(jù),將這三個(gè)數(shù)據(jù)平均后計(jì)算出該溫度下熱電阻的阻值,同時(shí)計(jì)算出傳感元件的工作溫度和環(huán)境溫差。實(shí)驗(yàn)數(shù)據(jù)見(jiàn)表2所示。
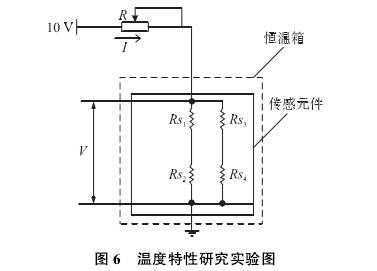
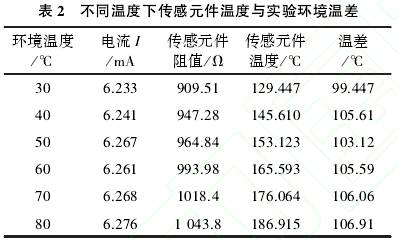
從表2可以看出,在電流恒定時(shí),環(huán)境溫度越高,傳感元件溫度也越高,但是與環(huán)境溫度之間的差值基本恒定在100 C,此時(shí)傳感元件靈敏度高且電流小而不會(huì)對(duì)傳感元件造成損壞,以此作為設(shè)計(jì)測(cè)量電路的依據(jù)。
4傳感電 路設(shè)計(jì)
一種新型的流量傳感電路,如圖7所示。傳感元件由熱電阻R, R,R、R,、R.,構(gòu)成,與精密電阻R2、R3、R.、Rs、R。構(gòu)成惠斯通電橋,該電路能實(shí)現(xiàn)溫度補(bǔ)償,并能檢測(cè)管道中氣體的方向。電路中精密電阻R2與熱電阻R并聯(lián)不僅防止通過(guò)R..的電流過(guò)大,而且可提高溫度補(bǔ)償?shù)臏?zhǔn)確度。為了使傳感元件輸出與氣體溫度無(wú)關(guān)的穩(wěn)定電壓,理想情況下在任何環(huán)境溫度下應(yīng)滿(mǎn)足式(9)。
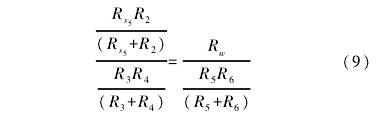
工作時(shí)將氣體傳感器放入測(cè)量管道中心,當(dāng)有微小氣體流過(guò)時(shí),上游熱電阻R,,、R..的溫度下降比下游熱電阻R,、R明顯,氣體將上游的熱量帶到下游,熱電阻溫度場(chǎng)變化引起電壓信號(hào)V2變化,V2反應(yīng)了微小流速氣體的流量。當(dāng)管道中有中高流速氣體通過(guò)時(shí),熱電阻R,、R,、R,、R.構(gòu)成的熱電阻R。的熱量被氣體帶走而引起阻值變化,從而導(dǎo)致傳感電路的電流發(fā)生變化,熱電阻R。用于溫度補(bǔ)償。通過(guò)測(cè)量熱電阻R。R,.和精密電阻構(gòu)成的惠斯通電橋的輸出電壓V,即可反應(yīng)此時(shí)管道中氣體的流量。

5氣體流量實(shí)驗(yàn)研究
運(yùn)用鐘罩式氣體流量標(biāo)準(zhǔn)裝置進(jìn)行氣體流量測(cè)試。裝置運(yùn)用鼓風(fēng)機(jī)進(jìn)行鐘罩的充氣,三個(gè)閥門(mén)用于控制氣體流動(dòng)。該設(shè)備的測(cè)量不確定度為0.5%,其能夠供給的流量范圍為0~220 m'/h。設(shè)備原理圖如圖8所示,實(shí)物圖如圖9所示
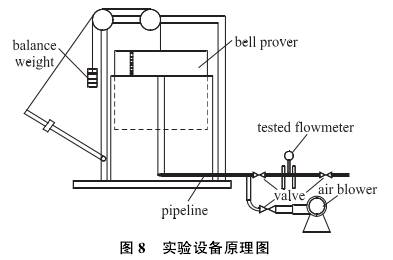
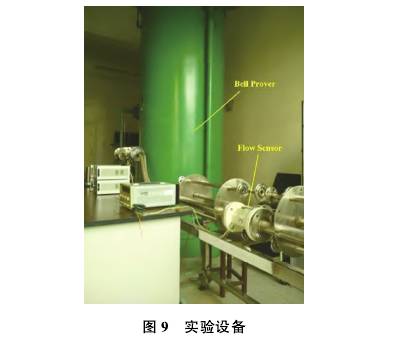
按照表1的仿真結(jié)果,本實(shí)驗(yàn)選用評(píng)價(jià)值相差較大的兩個(gè)傳感器進(jìn)行實(shí)驗(yàn),即傳感器1和傳感器9,其對(duì)應(yīng)的開(kāi)孔尺寸分別為寬3高9和寬5高11。
由于不同的流量范圍測(cè)量原理不同,流量測(cè)量實(shí)驗(yàn)分為2部分,其中小流量的測(cè)量范圍為0.405m'/h~2.841 m'/h。在不同的流量點(diǎn)對(duì)輸出電壓V2進(jìn)行三次測(cè)量,獲得流量與平均輸出電壓的關(guān)系曲線如圖10所示。傳感器1在小流量測(cè)量中,不同流量與輸出電壓關(guān)系為星形點(diǎn),測(cè)量重復(fù)性最大值為0.5%。傳感器9在小流量測(cè)量中,不同流量與輸出電壓關(guān)系為圓形點(diǎn),測(cè)量重復(fù)性最大值為0.8%。比較傳感器1和傳感器9的輸出特性,可知傳感器9由于開(kāi)孔略大,輸出的電壓值略微偏小,而且重復(fù)性略大于傳感器1,與仿真的結(jié)果相同。

隨著流量增加,對(duì)傳感器在2.841 m'/h至130.3 m'/h范圍內(nèi)進(jìn)行流量實(shí)驗(yàn)。在不同的流量點(diǎn)對(duì)輸出電壓V進(jìn)行三次測(cè)量,獲得流量與平均輸出電壓的關(guān)系曲線如圖11所示。傳感器1的不同流量與輸出電壓關(guān)系為星形點(diǎn),測(cè)量重復(fù)性最大值為0.5%。傳感器2的不同流量與輸出電壓關(guān)系為圓形點(diǎn),測(cè)量重復(fù)性最大值為1%。如圖11可知傳感.器9的輸出電壓值略微偏小,與表1的與仿真的仿真數(shù)據(jù)相吻合。
傳感器1具有較好的輸出特性和測(cè)量重復(fù)性,與仿真結(jié)果--致。因此,以下對(duì)傳感器1進(jìn)行具體分析。
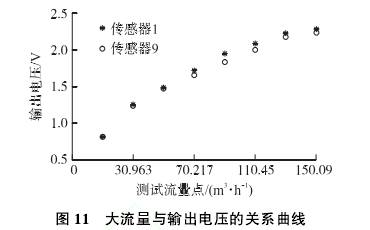
運(yùn)用MATLAB擬合電壓與流量之間的關(guān)系公式[ 16],得到傳感器1的數(shù)據(jù)模型:

式(10)和式(11)所示的數(shù)學(xué)模型分別用于測(cè)量小流量和大流量。通過(guò)擬合數(shù)值和輸出電壓可計(jì)算得到最大偏差A(yù)mre由式(12)可計(jì)算得到擬合Lmax誤差γYL°

其中ym為最大流量點(diǎn)的電壓。在小流量時(shí)擬合誤差為1.42%,而在大流量時(shí)為1.40%。由于傳感器1的重復(fù)性最大值YR均為0.5%,由式(13)可以計(jì)算得到測(cè)量誤差.

由式(13)可得在小流量范圍內(nèi)最大測(cè)量誤差.為1.50% ,在大流量范圍內(nèi)為1.49%,由此可認(rèn)為測(cè)量誤差為1.50%。對(duì)造成誤差的主要原因有氣體擾流,流場(chǎng)分布和氣體濕度等。另外,傳感器的熱輻射和熱傳導(dǎo)同樣會(huì)造成測(cè)量誤差。
由實(shí)驗(yàn)可得,傳感器能夠在0.4 m'/h至130m'/h的范圍內(nèi)測(cè)量氣體流量,其重復(fù)性?xún)?yōu)于0.5% ,測(cè)量誤差為1.5%。
6結(jié)論
熱分布型和浸入型相結(jié)合的熱式流量測(cè)量方法,設(shè)計(jì)了一種大量程氣體流量傳感器。通過(guò)FLUENT仿真技術(shù)和權(quán)重法確定最佳傳感器的結(jié)構(gòu)模型,研究傳感元件的溫度特性,提出了氣體介質(zhì)溫度的自動(dòng)補(bǔ)償方法并設(shè)計(jì)流量傳感電路。實(shí)驗(yàn)結(jié)果表明,該傳感器測(cè)量量程為0.4 m'/h~130n2/h,測(cè)量誤差優(yōu)于1.5%,擴(kuò)大了熱式流量傳感器的流量測(cè)量范圍。
以上內(nèi)容源于網(wǎng)絡(luò),如有侵權(quán)聯(lián)系即刪除!